Thursday, April 14, 2011
COLOR MANAGEMENT / MANAGEMENT IN COLOR OFFSET PRINT
Standardization is required in each discipline, although there was a relationship with one another. Graphic design, especially those associated with printing, offset, print, has a different standard to other branches of design.
Small things sometimes forgotten by a designer when creating artwork for the preparation of offset printing. They've learned a lot about color theory, typography, psychology, communication. But they did not pay attention, whether they already meet the design standards for offset printing. From the visual side of good, a good concept without memadahi based on knowledge of print preparation (pre press) could result in the failure of a design masterpiece.
I take the easiest example is the standard color. It takes little in-depth understanding of color, what color system used in offset printing. Because there are differences in every field of design, is the most common color system RGB, CMYK, and color hex plumpness for website creation.
In this article I was little mention of the color management / color management. Because so many designers are now less understanding about color management. Even the color system dipakaipun sometimes wrong.
We've struggled to create captivating design, a luxury, but when printing received complaints from consumers. Of course we do not want this to happen to us. Moreover bear the losses from the mistakes we make. Consumers protest because of the color printout is different from when we ACCkan.
Proof
It is very necessary to deal with mistakes, harmonize consumer desires with what designers intended.
Proof Type:
1. Design Proof
2. Proof Contak
3. Page Proof
4. Imposition Proof
Proof-ing has several purposes, generally as a consumer desire to harmonize the process with the designer, as a standard color reference.
Color Management
Proofing is part of the standard color, the color intended to print to meet the expected standard, consistent, and measurable, harmony between the print colors, monitors, and proofing.
The problem that often arises is the lack of match between proofing, monitor, and print output. There are several factors that cause these things happen. Factor, printing inks, printing machines, and paper. Each type of ink and paper has a different character.
In addition, the input process, namely basic materials also determine the final outcome, whether from repro, digital photos, or other media. Will influence also on the printout.
Solutions to minimize error is to use measuring devices, calibration of all equipment (monitor, scanner, printer) and color chart / finder.
Friday, April 8, 2011
Effect of Engine Calibration PrePRESS In Improving Print Quality

How much influence the design of the mold?
what is the impact design with different software-software ..?
is there any standard software of the printing press because there are some who design software available today?
To design, in fact that often the problem was the designers hope, so that designs can be printed as closely as possible with as imagined.
Well, the condition of the engine that's different, let alone get to the engine offset (web / sheet feed), want to Imagesetter or plate setter course there must be degradation if we do not know the characteristics of the engine.
Any software engga there is a problem. The most elaborate example today is to overcome the transparency / Flatten Image
the type of vector, bitmap file reply is usually safer ...
Well, if if is working on the prepressnya, we own, we'll know we tuch RIP capabilities, but, if thrown out, wait a minute, not necessarily.
Image must be "tuned" according to its web engine capabilities, both in terms of speed and print capabilities.
When we design, we've set as expected on a web machine, but we forgot our image setter also has a share of the display. The result, so keep baseball as expected.
Indeed, for digital printing, because fewer variants to be more simple ... from workstation designers can directly or via PDF directly to the RIP, his server printer.
Meanwhile, if we use the offset, the variant is more diverse and that determines the ability of the engine also supported by some of the items ... it is a little more should be known by the designer for not often disappointed by the outcome. If the problem recommendation software .. may generally adobe freehand family ... also have been purchased by Adobe.
And at Adobe has also been boosted with enough color profiling system that is quite okay for print needs.
in order to WYIWYG ... what you see is what you get.
Regardless of the engine or printing method, if you want more designs save printing, variants that will be passed we need to know the details.
For example if want to be outsourced or given to a printing firm, which became the benchmark is usually the result of proofing that he love, with its assumption of the proof engine is adjusted profile with the capability of printing machines which would be used.
Why is that? ... printing machine was khan of the most expensive and big, so updates take the longest, the profile that we use so that we reference in reading the limitations of printing capabilities.
If the limitations of the machine which we will use it can be read on the front, designers become more 'confident' to make his designs.
So do not blame the printing machine, if the print does not match ...
This will be much better, if we make a film myself and nyetak own ... because we would understand the true condition of the machines that will be passed by the job earlier.
Design Standards.
Of course with the tools and their parameters, such as
- Standard color (color reference guides, Pantone, tc, etc)
- Standard composition of colors (color gamut)
- Understanding error hue (color irregularities)
- Standard error delta (Color Management)
- Good way to see the color (lamp, tld 65, etc.)
RIP-plus again he started the version number?
Why is that?
If his baseball RIP directly attached to the computer designer, designers usually will to save his job level with its software version.
For example = Pake Indesign CS4, but it is still old school which RIP version postcript not use PDF, models such as this, the result is really unpredictable
because of the ability of interpretation RIPnya jadul khan, while software designs have much higher knowledge ....
In the computer designer, cool design view ... so the RIP, image and text is a pockmarked, there is a misah, some piled .. things like this that must be addressed.
Calibration and profile making all the equipment we used during the printing process, should be performed.
But many actors who would do this mikirnya very long. For those who fully understand their function, they will be well aware, but which ngertinya half, certainly horrified really ngelihat 'waste' that will be wasted.
Calibration was actually working for as much as possible restore the ability of each machine to be as optimal as possible. For CTP and CTF machine usually over time, the laser has decreased the ability, so engga linear again. Well, CTF or CTP is if we want to create a reference, should be in the linear condition. What is linear sich? ... That Linear raster condition of 2%, discharge, O 2% in film or plate, 3% O 3% & and so on. After it goes wrong, we try new dech see the condition of the printing press. We make reference. We'll see how the machine to interpret the image. There is a dot gain .. we see the ink, flat or engga ... the things we fix it ... then after okay .. we have just stepped into the profiling that enables workstation designers can know the condition of the produksinya.Menutrut experience hell ...
Calibration was actually working for as much as possible restore the ability of each machine to be as optimal as possible. To CTP or CTF machine usually over time, the laser has decreased the ability, so not linear anymore. Well, this CTP CTF ato if we want to create a reference, should be in the linear condition. What is linear it ... the linear raster condition of 2% O 2% at discharge ato film plate, 3% O 3% etc. ... After it goes wrong, just deh try nangkep condition of the printing press. We make reference ... na we see how the machine interprets the image. There Ntar dot gain ... ato mean we do not see ink ... na ... the things that we benahin ... okay ... then after we have just stepped into the profiling of memungkinakan workstation designers can "know" the condition of its production ...
Not the CTF and CTP course you know who skip the calibration process ... all monitors, scanners (if you still use), proofer (also if any) should also through the calibration process. For example on the monitor, the monitor light day we will increasingly shift its light color ... of which had been okay, so it looks more green or red ... because the value of the RGB phosphor provider starts to diminish its light color in there. Well, in this condition the user should also know ... there are tools to determine the value of Kelvin the light of the monitor.
plate / film linear key for machine calibration, meaning that can be used as reference to find how much the mechanical dot gain our printing machines. If you've met profile machine (dot gain, density), then the machine data can be made a reference to the calibration proofer. So, what can later be issued proofer in akomodir / achieved by our printing machines, the color will be very small deviations occur. Advertisers or customers will know more once the results, like what before printing. Phosphor RGB color giver of light began to decrease in situ.
Na ... This condition of the wearer should also know ... there are tools to learn the value of the light monitor Kelvin.
Mean obviously there are things that must be bridged between the ability of printing and imaging capabilities of prepress plate.
interesting to discuss the WASTE that may occur during the process ... yes Dlm calibration process?
To Waste ...
The earliest is from the movie auto plate CTP or CTF. When we checked the linear machine, depending on the condition of the engine ... we are definitely checking allignment laser, sometimes here could be a few plate / film that we output a perfect allignment until we can get.
Then a new step into the raster. We have to check several times exposure to check its density. For the film, we first check its density image, we use a step to the plate FOGRA .. this depends on the type of plate is also .. for photopolymer for example, we usually use two third dark shadows, etc ... each plate from different vendors is also setting its exposure.
After exposure to new dech wrong ... we see the percentage of raster. 2% of its out how to 99% & a lot of precision measuring instruments that can measure the value raster ranging from 2% to 98% only. But, that should suffice.
From prepress machine that can be imagined khan how much should we output. Especially to the standard engine sparse. Kalo aja destitute just done.
Many customers are very conscious of the value raster, do it at least 2x a day, at the beginning of work (shift1 and second shift) ...
After the prepress is complete, we created a new reference image which we will print. Usually it consists of many color patches to create a profile of printing machines and all machines proofer.
Well, when we last checked in on the value raster prepress machine, etc. .. It has not been associated with the workstation, but purely from the engine.
Now, because we send the reference image .. we see again in CTF or CTP result ... after a measured completely linear, we continue to dech new printing machine. image which we will print. Usually it comprises so many color patches to create a profile of printing machines and machines proofer all ... maybe one time I'll try to post examples of reference image for the calibration and profiling yah ... (But which can be posted yach ?)...
Well, when we last checked in on the value raster prepress machine, etc. ... was not related to each workstation, but purely from the engine.
Na ... now because we are sending a reference image ... we look again at CTF CTP results ato ... after the measured linear bener, we deh terusin new to the printing press ...
Having reached the printing press ... we just started to involve other waste more ... paper, ink, etc. ... Often that had a machine, nyetak origin same thickness of ink already in the parts of the image that has been marked, it is equal ... stopped ... but ... stability of ink that's different backgrounds on each machine and its length depends on the run as well, sometimes we can see other parts of the printout is still less ink, etc. ... but the engine had stopped. Because it can be imagined, the paper has been kebuang how much ... and again, they certainly can not do another job ...
It's in the press ..
Then, after the printing machine goes wrong ... we get results ...
We stepped into the proof engine.
Any process that we went through last ... we'll never be able to see the same gamut ... although both CMYK.
Well, calibration for machine proof is a bit more proof that our paper output.
First ... we must determine the UCR and GCR that fit for us so that if the proof machine black mold proofing color is not white but can be bluish or redish black puree and gradation.
After that new dech, we stepped into the color. This proof machine khan prepared to represent a wider color gamut of all the machines that we use from the work station until the printing press .. nah, we must reduce gamutnya so he can represent the colors that can be printed by the printing machine.
Especially for the image with the colors of the process ..
Not to mention the machine proof we will often find the results with the image bending, .. nah, kalo udah no bending lines ... khan results are not perfect ... things like these that make wastenya so make this proof ngeri.Mesin khan prepared to represent a wider color gamut of all the machines that we use from the workstation until the machine print ... nah, we must reduce gamutnya so he can represent the colors that can be printed by the printing press ...
although its a lot of waste during the process of calibration and profiling (often well done) ... more done gentlemen, do not be payable. Because its going to waste even more.
Or if a half-half, the result will not be good ... such as that had submitted, for fear of spending a lot of paper, ink is so thick in places marked are okay, straight stops, but on-it still is a striped, continue to be forced measured, well, you can imagine the results. Not the expected results in the future, these results could be a benchmark baseball ... eventually waste which was already much more so bener2 wasteless.
Listen
Read phoneticallyDictionary - View detailed dictionary
Thursday, April 7, 2011
Next generation thermal CtP - Heidelberg Suprasetter


Signaling its commitment to CtP solutions, Heidelberg has released its new family of Suprasetter machines that are characterised by innovative technological enhancements and potential for upgrading.
The new Suprasetter family is a thermal CtP range that was completely developed and produced within Heidelberg. Designed with a strong focus on modularity and upgradeability, the Suprasetter will grow to meet increasing demands and protect the customer's investment.
Together with the Prosetter family, Heidelberg now offers one of the most up-to-date product lines on the market.
Imaging technology from Heidelberg
The laser head offers excellent potential for boosting plate throughput. The Suprasetter models in both format classes are available in configurations going up to a productivity level which can justifiably be termed “high-speed”. Subsequent upgrades are also possible at any time without needing a long period of downtime. In order to ensure rapid and completely reliable plate imaging, one thing is absolutely vital - intelligent laser systems that can be relied on. Each module is equipped with 64 laser channels. The Suprasetter laser head is comprised of two to six modules, depending on the product specification.
The Intelligent Diode System (IDS) ensures that operation can continue even if a diode fails due to wear and tear. In any given situation, the IDS automatically looks to the left or right of the failed diode to find the largest possible group of active diodes, and then continues the work with these. Alongside the IDS, the depth of focus function ensures constant production reliability. The new Heidelberg laser system thus guarantees a high standard of imaging quality, automatically compensating for any unevenness in the plates.
Suprasetter Family
With the new laser developed by Heidelberg, excellent imaging quality and increased productivity isn't all that you should expect; you can also add new modules for a boost to the speed of your throughput. The modular design allows for a tailor-made range of configuration options to suit any requirement. Moreover, the performance of a Suprasetter can be enhanced on the spot at any time by adding laser modules. Thanks to its compact design, upgrades can be carried out without lengthy periods of downtime and with minimal service intervention.
Temperature stabilizer
The Suprasetter does not only offer excellent plate production independently of its technical environment. Thanks to its integrated temperature stabilizer, it can also deal with any temperature changes which might affect output quality. This keeps the temperature inside the device at a constant level, preventing any expansion or shrinkage of the aluminum printing plate which might cause register inaccuracies. This means that a Suprasetter can be operated under a very wide temperature range from 17° to 30° C (62.6 to 86° F).
Top punching precision
The Suprasetters were designed to create top-quality print-ready plates with a minimum of time and effort. In order to achieve this objective, an efficient and precise internal punching system was essential. The new punching method used in the Suprasetter ensures that punching is performed with a register accuracy of +/- 25 µm for all printing presses from Heidelberg, as well as for most other printing presses available on the market. Additional punch types can also be added at any time in the future as field upgrades.
Automatic operation with Single Cassette Loader (SCL)
The Single Cassette Loader that connects onto the back of the Suprasetter is the first step towards fully automatic plate production. After removing the slip sheet, it loads the plate into the Suprasetter for imaging and then outputs it via the online processor connected to the side of the device. Since the plate is inserted with the narrow side first, a processor with the smallest possible entry width can be used. This really pays off in terms of low purchase and running costs, as well as saving space. Alternatively, you can continue to produce manually or semi-automatically with full convenience.
Fully automatic production with Multi Cassette Loader (MCL)
In its highest configuration level with MCL, a Suprasetter definitely holds its own in terms of versatility. The MCL consists of the SCL plus a docked plate container, and can hold up to four cassettes. Cassettes are selected fully automatically, depending on the job.
Smart plate handling
The Suprasetter also offers the option of convenient manual operation or semi-automatic production, even if you choose the highest configuration levels with an interfaced SCL or MCL. This is no problem, since - unlike other CtP systems - a loader is docked onto the back of the Suprasetter. This leaves the plate table on the Suprasetter freely accessible for manual plate loading. This represents a big advantage over competitive systems, most of which only permit limited bypass operation. With the Suprasetter, fully automatic and manual operations are not mutually exclusive - they are instead two different practical options offered by the single system.
Centered and Edge Registration for running Sheetfed and Web presses
Sheetfed presses need centered registration while web presses need edge registration. Customers with both press types want to have only one CtP to image all the plates for their presses.
Prepared for Processless Technology
Imaging Technology from Heidelberg comes equipped with enough power to image low sensitivity processless plates. Thus all new plates that will be available on the market will be tested.
"Plate on Demand". The connection to the Prinect CP2000 Center*
The Suprasetter can be integrated seamlessly into a workflow that features the Prinect CP2000 Center. This allows the operator in the pressroom to launch plate production without any specialist prepress knowledge, simply by selecting the plate for imaging from the list on the Prinect CP2000 touch screen. The output order can be changed at any time.
Wednesday, April 6, 2011
International Standards for the Printing and Media Industries ISO
International Standards Organization (ISO), founded in 1947, is a worldwide federation of national standards of more than 140 countries (one country represents a single national standard.) The mission of ISO is to promote the development of standardization and related activities in the world in terms of provision of exchange of goods and services at international level and to develop cooperation in intellectual activities in the environment, science, technology, and economic activity. Performance ISO set forth in international treaties and published as International Standards.
Members - Members of ISO
ISO is made to its members who are divided into three categories:
Member Body
Members of ISO is a national body "main standardization in its country representative."
For each state is recognized only one membership of ISO. Members are given the right to participate and have full voting rights in the technical committee and policy committee of ISO.
Members - Member Contact
Members of correspondence usually is an organization in a country that does not have a comprehensive development of national standards activity. Correspondent members not actively involved in technical development work and decision-making, but was assigned to provide comprehensive information about the work of ISO in the country.
Members - Member Subscribers
Members of designated customers for the country - low berekonomi country. Member subscribers pay reduced membership fees that do not allow them to maintain ties with international standards.
ISO Strategy
International standardization can be used in a variety of different technology fields such as information processing and communications, packaging, distribution of goods, energy production and utilization, banking and financial services, and increasingly considered important for activities in all industrial sectors.
The main reason is:
• The development of the world toward free trade
From the technology side, fair competition should be based on the ability of identification, be clearly identified on the basis of a common reference that can be recognized by any country or region. Applicable industry standards widely known internationally, was developed from consensus among traffickers, presented as a trade language.
• Linkages between sectors
There is no industry in the world who really independent or not depends on the components, products - products, rules - the rules of application, and others that have been developed in other sectors. Eco-friendly products and processes, and has the capability of recycling, or packaging that easily broken down, has become a widespread concern.
• global communication system
Computer industry to give an example - a good example of technology that is needed quickly and progressively to be standardized at a global level. Full compatibility in an open system encourages healthy competition among producers.
• Global standards for high-tech
Standardization program in the new field as a whole is currently being developed. The need for standardization is to define terminology and accumulated a database of quantitative information.
• State - developing countries
Continuous development agency to introduce that a standardization infrastructure is a necessary condition for successful economic policy in order to achieve sustainable development. Creating the infrastructure in the countries - developing countries is very important to raise niali productivity, market competitiveness, and export capability.
Generally accepted industry standards is a condition conducive to the particular industrial sector because most of the products and services have the same conformity to standards. This condition is achieved due to the consensus among economic actors, the industrial sector-suppliers, users and government.
The ultimate goal is the implementation of trade, exchange and transfer of technology through:
• Improved product quality and trust at a reasonable price;
• Improved health, safety and environmental protection, and waste reduction;
• Improved compatibility of the components of goods and services;
• Simplifying the level of usage;
• Reducing the number of samples and also the reduction of expenditures;
• Improving distribution efficiency and ease of maintenance.
Agency responsible for the printing industry standard is the ISO Technical Committee 130 and Graphics Technology secretariat of this body are in DIN (German Standards Institute) in Berlin, Germany.
“ PRINT ON DEMAND “

In the past, every time you publish the book, the publisher should print at least 3,000 copies to save on printing costs. Now, with advances in technology, print on demand, printing costs can be saved and the number of copies can be met on request.
Print On Demand (POD) is one result of the advancement of digital technology. Computer technology plays an important role in this system and the POD is a printing process that formed due to digital printing (digital printing). Through digital printing, a particular stage must be done on conventional printing systems is no longer needed. Because the process simpler, then digital printing allows people to save costs and time for the amount of a particular print.
Conventional Print
Conventional printing system-the so-called offset printing has a chain-long process. In a simple process that is divided into two: pre-print and print (pre-press and press). The person preparing the art-work or manuscript in pre-printing process. If the manuscript is a manuscript book, after going through the editing stage, it takes stylists-Lay (lay out). When finished set, otherwise print-ready manuscript (camera ready). Why is it called camera-ready? Because it means that the script is ready to be recorded with a camera aka photographed. The contents of the manuscript is recorded into the sheets of film. The next process is to move the contents of the script of the film sheet onto the printing plates.
Print process starts after receiving the printing plate or a print copy. With the printing plates that printing begin the process of printing on an offset printing machine or machines. Because the use of film and plates, the offset printing requires a certain amount of circulation for the print or print cost per book is not to be too expensive. From this arises among publishers term "curse of 3,000 copies" because usually the publishers need to print a book with the minimum amount of 3,000 copies for the book found an economical price.
Digital Print
In digital printing, printing no longer need to record the script into a film and plates. Print-ready manuscript, can be directly printed on the printing press. Why is that? Because digital printing machines work by accepting the manuscript (printed materials) directly from the computer, without the need for printing plates. Printable text file on the computer are sent directly to the machine for printing, such as if you print data from a computer using a desk-jet printer or toner. Film and plate-making process that takes time and costs are no longer needed. This means basically no minimum amount required to print. Printing can be done with the script and the budget amount that suits your needs and pocket size. In essence, digital printing is more economical and efficient for a small circulation. That's not all the features offered by digital printing. Author or editor can also alter or improve the manuscript in the final seconds of the print process. Such flexibility is risky if done at the cost of conventional printing as improvements to the manuscript to be printed means the replacement of film and printing plates, in addition to the work it takes longer.
Comfort with POD
For Publishers By providing ease of printing through digital printing, then the next thought developed among the managers of the book publishing business is "Why not print as needed or market demand?" He replied: "It could have been done." Manifestations of the above is what the desire called print on demand (POD). Why is it called on demand? Because we can print on demand or requirement. There is no longer mandatory ("curse") a certain amount in print. Need print 100 copies? OK! If 50 copies? Monggo! 10 copies? Who's afraid? Requests can be served. Thus, what are the implications for publishers or anyone who wants to print a book? Publishers can save the investment in inventory. Published a new book-the unknown market potential-can be printed with a limited number first. If the book is "exploded" in the market, the publisher can print them in large quantities. Similarly with the book reprinted the life cycle (life cycle) it has begun to fall. The book can be printed on demand market.
The market for only 20, the issuer can meet them without having to worry about stock piling up in warehouses because of excess printing. The next circle of POD comfortable is the publisher can save money warehouse. There are no stock piles of books idle, meaning the publisher does not have to always add to the warehouse. This fun story can be drawn on until, for example, that because they do not have to invest money in inventory investment many books, so publishers can publish more titles, that cash flow (cash flow) publisher become aliases is not blocked more smoothly bin smoothly.
For Writers Well, if you are a beginner writer who had long "revenge" against the publisher because you rejected manuscript back and forth, POD opens opportunities for you. You can now publish your own book. This means you can become independent publishers aka indie. With POD, you can print your book economically, according to budget. For the writer, POD will allow you to determine your own fate manuscript-probably also the fate of your rice pot. If you have previously hampered many writers to the new birth as a writer, now there is a scalpel that allows authors to Caesar for the script. You not only can accelerate the inclusion of the profession as a writer on business cards, you can maintain the integrity of your manuscript.
Tuesday, April 5, 2011
Separasi Pecah Warna untuk Sablon
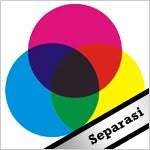
Sebelum kita membahas hal ini perlu diketahui hal berikut :
a. Harga sablon tergantung jumlah warna karena disitulah point berapa copy ( kertas sablon ) dibuat
b. Copy dibuat berdasarkan pada jumlah warna yang dipakai dalam satu karya desain, misal : ada warna hijau muda, hijau tua, merah, oranye dan hitam maka umlah copy adalah 5 buah
c. Proses mencetak ( print ) berbeda dengan proses sablon. Proses cetak adalah menimpa titik kosong dan titik warna basah dalam mencampur warna. Proses sablon kita akan mencampur warna dasar ( CMYK / RGB ) untuk menghasilkan warna sesuai desain yang kita buat terlebih dulu kemudian memasukkannya dalamcopy, oleh karena itu kita harus membuat katalog warna dalam desain kita.
d. Sangat dihindari warna gradasi karena proses pembuatan rumit untuk sablon, trasparansi ( transparent ) jika ada maka gradasi diganti dengan warna blok dan transparent diganti warna fill substitusi.
Pecah Warna
1. Buka karya desain Anda dalam area kerja coreldraw (ingat objek yang dibuat harus bisa diedit oleh coreldraw / buka hasil import yang tidak bisa diubah oleh coreldraw, ex: eps; bukan berupa bitmap/raster). Menu File >Open untuk membuka hasil desain Anda atau Menu Import untuk mengambil objek desain basis vektor.
2. Tentukan warna maksimal, contoh 3 warna merah, hitam, dan kuning. Jika ada warna diluar warna diluar warna yang ditentukan ganti sesuai dengan warna tersebut.
3. Buat halaman baru pada area kerja sesuai jumlah warna yang akan dipecah, contoh 3. Rename / ubah nama halaman baru tersebut sesuai representasi warna yang ada contoh: merah, kuning, dan hitam. Letak ada di bawah lembar kerja.
4. Copy objek desain Anda dan kopikan ke setiap halaman baru
5. Edit dan delete objek yang tidak direpresentasi oleh nama halaman yang baru Anda buat. Contoh pada halaman merah maka, selain warna merah tidak diperbolehkan warna dan objek dari warna itu ada. Pertama kali yang diedit dan disesuaikan dalam proses pecah warna untuk sablon ini diutamakan warna background/ dasar. Karena backgorund adalah warna yang akan ditimpa oleh warna/objek lainnya.
Proses pemotongan adalah cara yang paling sering dilakukan pada objek warna dasar. Untuk pemotongan klik / pilih objek menggunakan pick tool dan Shift + klik pada obje kedua. Tekan tombol trim
Lakukan proses diatas berulang hingga menghasilkan warna merha saja yang ada
6. Ulangi cara pada no lima pada setiap halaman yang baru Anda buat. Karena background adalah warna yang akan ditimpa, makan untuk warna kuning dan hitam, kita tinggal delete warna selain warna representasi dari halaman.
7. Hasil siap di cetak pada kertas sablon
Monday, April 4, 2011
Film Making Process Separation
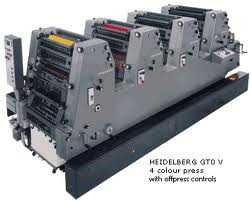
The process starts with receiving digital data from the customer in the digital image is usually directly from a digital camera or photo to be scanned.
The digital data is then opened on a PC to be checked for non-completeness problem occurs with the output movie.
Then the data made into a data postscript or PDF file and in output to Imagesetter (CTF) through the RIP (Raster Image Processor), for a film separation.
Then through platemaker contacted a printing plate and ready made progressive proof
The steps that must be done:
1. always the best possible preparation for the original image here termed garbage In .. Garbage out .. (Kalo yg processed image with low quality (small file size .. just a 72dpi resolution) then the resultant production would surely be less good his jg ..
2. using Photoshop software to process the gambargunakan potoshop for image processing will be in use for print production. Other software such as windows picture and fax viewer or Photopaint is not recommended.
3. RGB to CMYK conversion
this is very necessary dlakukan.Mengingat no ato digcam bbrp scanner working with RGB color, often a decline in color from RGB to CMYK. how far they will first decrease due to the difference between the RGB colorspace CMYK dmn n greater drpd RGB colorspace CMYK
4. image resolution
its image resolution is bnyk distinguished elements form an image. dmn magnitude certify Dlm ppi (pixels per inch) ato dpi (dots per inch).
to know the input resolution for print auspicious,
dgunakan verifiable formula: 2 x screen ruling. if the screen ruling which in use is 150 LPI then menjd 300 dpi input resolution
jg pd ruling screen printing often as raster dsebut .. ato screen frequency. This influential paper type yg pd later would be in use for printing.
5. digital image analysis and correction of the most important:
* Specify the highlights (white point) and shadow (dark point) way by using the menu ato curve pd level photoshop
* Color cast (color bias) bias is often not desired color, eg Yellowish color (yellow), redish (redness), bluish (blue).
how to get rid of this color is a menu with the curve, color selective color balance ato
* Tone (contrast color - to avoid the image looks 'flat' - flat) way with the curve menu (fix the midtone) * correction warnacaranya can use selective color menu
* Sharpness / sharpness interchangeable with Unsharp masking6 menu. file format
* Tiff (tagged image file format) is a non-compressed file format to preserve the completeness of data recorded color reply
* Eps (encapsulated postscript) format interchangeable inin dgunakan to send bitmap image information postscript dr one prog. k prog. other. dpt dterapkan pd vector drawing bitmap atopun
* Jpeg (joint photography expert group) files for its ud kkompres high mobility of data and practical
* Dcs (explanation for this distinguished bnr2 more k-way printing machine n CTP)
* Pdf (portable document format) is the file format used timeout smua dbuat n jobs are ready for the d output.
its advantages are: interchangeable compress data with good quality, and is cross platform dpt dbuka shingga both PC and macintosh d ..
7. do not forget to link imagestlh we make a design, gather images in 1 folder with dmikian its own would not have happened during the missing link output
8. textteks do not forget .. hrs d d convert to a path or create the outline .. ato his cool language .. 'Off' .. kalo bs not even dmatikan, which always include the type fonts in use in 1 folderbtw .. do not forget jg .. tlalu jgn small fonts .. because it would complicate the reading
9. vector drawing
* Make sure it is CMYK
* Discard element2 dperlukan yg ga .. suppose we'll make sbuah bodytext .. was ill .. tp jd nah .. sampah2 .. such as text area dbuang tsb hrs ..
* Avoid using the path which tlalu bnyk ..
* Make sure the color of our vector design in accordance with color chart ..
* Overprint is a process of coating colors blend dr an overprint object.tujuan done is to avoid it happening ..... miss register.tp if the use of incorrect overprint problem will occur.
as an example of this brikut:
- Black text with background warnakalo this type .. must be in overprint ..
because in the event miss register, will give rise to white text dsekeliling. krn color appeared on a distinguished background area dtmpt-i text not covered by ink (jd pd plates shift there this .. ksalahan fit the mold)
- Text color with the background color with the background color of text .. should not be in overprint color .. krn text color will join with the background color ..
- White text white text .. also not be in overprint ..
His simple example gini d. .. u pd PNH ato liat tabloid newspaper her text dmn his color fled ga tu? well that his text was gara2 dbaca n dcetak 4 colors by the printing machine .. souw .. dmn suppose the color of his td who wants only black .. (Only black 100%) found by the dbaca 4 color printing (CMYK) so .. no more, .. his friends that his name overprint
* Trapping is a method to avoid problems with printing d register to add shape to the edge of the object at 0:15 to 0:30 mm. dmn print at the moment it happened aj bs development shingga paper raises miss register, causing a 'white effect' which is in freehand diinginkan.menu not exist in: window> toolbar> Xtra operations> trapouw y.. This effect is very dperlukan when using spot color or special .. and also in the packaging industry his trutama gravure.gampang gini .. PNH u liat ato dmajalah newspaper / tabloid a picture of his distinguished edge there appears white right? nan who dnamakan miss it registers without trapping.
To assess the separation film is good film must always perform calibration on a regular basis to maintain the quality of the movie separasinya.
Measuring tool that is used to calibrate a densitometer.
Some thing hrs dr note to check the quality of the film separation, among other things:.
1.density: separation film thickness value.
Recommended maximum density value is 3.8 - 4.2 D.
To know the value of density of a film, using a measuring instrument densitomer hrs Transparency.
Low density value which will result in solid colors on your printed output will look faded or the color is not dark. One cause of low density is krn processor conditions are less good.
2. linearization dot (raster): raster 50% in digital files must be out 50% jg on film with more or less 2% tolerance
Basic Screening
Screening (or halftoning) is the process of drawing and color reproduction in printing. To complete this process, image or color should be broken up into patterns of dots called halftone screens (halftone screen). Simple application of this technique is approaching the level of gray with a pattern of black dots on a white background. Color shades can be approached if the pattern of four-point-color cyan, magenta, yellow, and black are used.
The points are applied in a proper arrangement and proportion. When you register, cyan, magenta, yellow, and black dots will form a rose pattern which is a "blend" together to give a great impression with a number of different colors.
Halftone dot-produced by the rasterization process of photographing the original image through a screen which is
The main function of raster image processors such as RIP HQ. Light reflected from the image creates a point in every hole in the screen. The size of dots on each particular point is proportional to the amount of light coming through the screen, the number of lines per inch that make up the screen determine the fineness of the point.
Each square in the grid called halftone cells, each halftone cell containing the point, which increases as the intensity of colors, which enhance the image of the picture. A point can take anywhere from 0 to 100 percent of the halftone.
In a black-and-white image, for example, points 0-percent white areas of the picture, the point is 100 percent black areas, and intermediate points dariukuran create the impression of gray area. Color images of work in the same way, except that three or four grid superimposed over the image in various angles. Each grid contains one color (cyan, magenta, yellow, or black, for example)
and called the film separation (separation film).
The process of CTP (Computer To Plate)

In accordance term direct-to-plate image-making process at the plate without using a photo reproduction of film-making process,
image printed directly on the plates directly from computer files. Digital files do not need to be changed or modified to several files
different because it is programed with RIPs systems, processes performed on all the filming done enough
using a mouse click and enter data via keyboard. The concept of making exactly the same berimage plate, according to the data file
designed / design but in a way that is totally different.
Excess direct-to-plate:
CTP plate production increases faster time, consistency and image quality of printed images. This method requires more time
Short of an offset lithography printing manner analogous because combining two processes into one. Manpower clear
reduced because no longer need to make photographic film reproduction. At least when we can save 20-30% with CTP. The resulting image
also more clear, sharp and accurate than traditional analog printing dot that appears for a cleaner and their image
The first - directly to printing plates, dot-gain effect is also reduced. Other savings from the material aspect that is less supply,
employees can be reduced and not use the camera more reproduce, so the less required space. These savings could
used as incentives for print and a factor price competition to attract new customers.
Lack of direct-to-plate:
Most people familiar with the images printed with dot-gain is large and looks darker. Not infrequently the customer will feel strange
with good results "unusual" is. Need for printing to provide an understanding of this new good stuff to the customer,
so accustomed. CTP is also the responsibility of changing the print quality of the original full-on printing, switching to "digital file creator" - people
which makes the image file.
Common problems encountered
In the lithography printing process, there are many possibilities to change or correct the wrong things in the movie. Not so on
CTP, printing operators should really guarantee clean image file. Consider the following things, save the file in CMYK format
rather than RGB, and use the exact specifications such as: (1) "bleed amount" appropriate, (2) make sure all the letters and high-resolution image
entry in the file, and (3) check the use of spot-color correct, etc..
The repair process of digital image files either in desperate need of a lot of time, which ultimately reduces excess CTP of analog film system.
Saturday, April 2, 2011
Workflow in Reprohouse
Workflow process begins with receiving digital data from the advertising / customer (currently all digital image is usually directly from a digital camera, so customers rarely bring [b] photo / slide [/ i] for the scan).
The digital data is then opened on a PC / Macintosh checked for completeness for non-problem occurs with the output movie.
Then the data they will be made into a data postscript or PDF file and in output to Imagesetter (CTF) through the RIP (Raster Image Processor), for a film separation. Then through platemaker contacted a printing plate and ready made progressive proof.
how to assess the separation film is good?
a fine day reprohouse must perform calibration on a regular basis to maintain film quality separasinya film. Measuring tool that is used to calibrate a densitometer.
There are several thing hrs dr note to check the quality of the film separation, including: register, density, and linerisasi.
1. density
film thickness is the value of separation. Recommended maximum density value is 3.8 - 4.2 D.
To know the value of density of a film, using a measuring instrument densitomer hrs Transparency. Low density value which will result in solid colors on your printed output will look faded or the color is not dark. One cause of low density is krn processor conditions are less good.
2. linearization dot (raster)
linearization dot raster means 50% of digital files must be out 50% jg on film with more or less 2% tolerance
progressive proof
is a distinguished print proof process done using offset printing system Dlm simpler shape and manuals.
progressive proof with proof jg often called conventional or manual proof.
Progressive proof is used as a guide color printing. This system is used during the workflow we still use Imagesetter (CTF).
The process of making the proof is done one by one as in a color printing machine.
When these conditions are less optimal proof engine and has produced ill again, so that spare parts are no longer supported by the vendor (manufacturer) and maintenance costs become more expensive.
excess Progressive Proof
1. More 'safe' when used as contract proofs because jg production using the same separation.
2. Simulation for printout actually closer because sama2 using the same printing components.
3. Special color for a very similar fit so the final production cost is quite expensive.
lack Progressive Proof
1. The process is done manually so difficult to make standard and less consistent.
2. Has a flatness problem in all areas of printing inks.
3. Colors which are not stable, so that each sheet has a different color.
4. Less efficient, because it still requires a separation film
5. Keep in a wide range of work space.
6. Production costs are higher, because the wear plate of raw materials, paper, ink, chemical and more than one operator.
7. The color of an image will be influenced by the surrounding dominant color.
When the color of the first progressive proof which does not match, the customer is generally asked is repeated.
Repetition usually done with the way they will:
First, replace the film and edit digital separasinya terlebi file first, or
The second way, still using the same film, but the amount of ink when printing progressive proof set, it is very easy to do considering all the process is done manually.
Digital Color Proofing
Not all Reprohouse provides digital color proofing. In general, only separation and progressive proof film.
However, in line with developments in technology, digital proofing, and enables more rapid color prints can be simulated as close as mgkn with digital proofing results.
Needs time which is faster and the efficiency factor for pushing an air-investment Reprohouse digital proofing
* Note *
Colors in the digital proofing a Reprohouse refers to the progressive color proof, which borders on progressive proof paper is limited to artpaper. HVS or newsprint which is not necessarily equal actual paper when printing.